Understanding the Effect of PET Resin Grades on Preform Durability
Learn how different PET resin grades affect preform durability and performance. Discover how a Plastic Manufacturing Company ensures high-quality PET preforms.

The foundation of contemporary plastic packaging is polyethylene terephthalate (PET), which is frequently used to create preforms that are subsequently turned into bottles and containers for medications, beverages, and personal care items. But not every PET resin is made equally. The strength, resilience to environmental stresses, and durability of the finished product are all significantly influenced by the quality of PET resin used in preform manufacturing.
For bottles and containers to remain intact throughout their lifecycle—from production and filling to shipping and end-user handling—preform durability is crucial. The mechanical characteristics of preforms are influenced by the inherent viscosity (IV), molecular weight, and crystallinity of the various PET resin grades. It is essential to comprehend how these resin properties affect production in order to achieve high-performance packaging solutions.
To satisfy industry standards and guarantee constant product quality, a plastic manufacturing company that specializes in producing PET preforms must carefully choose the right resin grade. The correct PET resin is essential for producing dependable and long-lasting preforms because it improves impact resistance, lessens deformation under pressure, and preserves bottle clarity.
PET Resin Grades and Their Properties
The intrinsic viscosity (IV), which reveals the molecular weight and chain length of the polymer, is used to categorize PET resin grades. Stronger mechanical qualities are associated with higher IV values, but better processability is provided by lower IV resins. The intended use, container size, and necessary performance attributes all influence the resin grade selection.
Lightweight applications like tiny water bottles and containers for personal care products frequently use low-IV PET resins, which normally have a density between 0.70 and 0.78 dL/g. Although these resins are easy to work with and offer outstanding clarity, they might not be strong enough for larger containers.
Medium-IV PET resins balance processability and strength, with values ranging from 0.78 to 0.85 dL/g. They are frequently used for bottles of carbonated soft drinks, where resistance to pressure is crucial. This grade maintains effective production capabilities while providing exceptional durability.
For heavy-duty applications like large water bottles, refillable containers, and hot-fill packaging, high-IV PET resins—which have a density of more than 0.85 dL/g—are necessary. Because of these resins' exceptional mechanical strength, impact resistance, and thermal stability, bottles are guaranteed to survive harsh handling and drastic temperature changes.
How PET Resin Grades Affect Preform Durability
Molecular structure, crystallinity, and stress resistance are among of the characteristics that affect a PET preform's durability. These characteristics are directly influenced by the resin grade, which affects how well bottles and containers work in the end.
Molecular weight is one of the main ways that PET resin grade influences durability. Longer polymer chains seen in high-IV resins strengthen the intermolecular network, increasing impact resistance and lowering the possibility of bottle deformation under pressure. Containers for carbonated beverages need to be able to tolerate internal gas pressure without losing their structural integrity, so this is particularly crucial.
Another important factor in influencing preform strength is crystallinity. The stiffness and stress distribution of PET preforms are impacted by resin crystallization during the stretch-blow molding process. Higher-IV resins have a tendency to generate a more homogeneous crystalline structure, which lessens weak spots and increases the bottle's resistance to mechanical stress. As a result, the finished product is stronger and more resistant to deformation and cracking.
Thermal stability is another important factor. Certain packaging uses, including hot-fill bottles for teas and juices, call for PET preforms that don't warp at high temperatures. Superior thermal resistance is exhibited by high-IV resins, which keep bottles from shrinking and keep their shape even when heated. This guarantees that bottles keep their integrity throughout their shelf life and during the filling and sealing processes.
When choosing PET resin grades for various purposes, a plastic manufacturing company needs to take these aspects into account. While preserving manufacturing efficiency and reducing material waste, using the appropriate resin guarantees that preforms fulfill durability standards.
Optimizing PET Preform Performance with the Right Resin
The first step in guaranteeing preform durability is selecting the appropriate grade of PET resin. Achieving consistent product quality also requires optimizing processing parameters. The way the resin reacts during production is influenced by variables like stretch ratios, injection molding temperature, and drying circumstances.
PET resin must be properly dried in order to preserve its mechanical qualities. Because of its high hygroscopicity, PET takes in moisture from its surroundings. Hydrolysis can happen if the resin is overly wet during production, which lowers the preform's strength and degrades its molecular weight. This problem is avoided by maintaining ideal drying conditions, which also preserves the IV of the resin and increases the longevity of the finished product.
PET preform strength is also influenced by injection molding conditions. To ensure uniform material distribution and avoid flaws like voids or weak spots, precise temperature control and injection pressure are essential. While too much heat might degrade the resin, too little pressure can leave the mold partially filled, which will change the consistency of the preform.
Another crucial phase in assessing the endurance of preforms is stretch-blow molding. Strength and flexibility are increased when PET molecules align properly, which is ensured by appropriate stretch ratios and blow pressure. Bottle failure is less likely when preforms with enhanced impact resistance and balanced stress distribution are produced by a well-optimized molding process.
To guarantee that every batch satisfies industry requirements, a plastic manufacturing company that specializes in producing PET preforms must put strict quality control methods in place. Preforms are guaranteed to retain their performance and longevity under real-world circumstances through routine testing of their intrinsic viscosity, impact resistance, and dimensional stability.
Advancements in PET Resin Technology for Improved Durability
New developments in PET resin technology are assisting producers in creating more robust and environmentally friendly preforms as sustainability becomes a major concern in the plastics sector. New developments like bio-based PET polymers and recycled PET (rPET) provide enhanced environmental advantages without sacrificing performance.
The production of PET preforms is increasingly utilizing rPET, which is made from post-consumer recycled plastic. However, because of previous processing cycles, recycled resin frequently has a reduced intrinsic viscosity. Additives like chain extenders and IV boosters are used to improve durability and restore molecular weight in order to get around this problem.
An alternative to conventional PET sourced from petroleum is the emergence of bio-based PET resins, which are produced from sustainable resources including plant-based materials. These polymers lessen their carbon impact while providing mechanical qualities comparable to those of traditional PET.
A plastic manufacturing company can promote sustainability objectives and increase perform durability with these improvements. Advanced PET resin technologies enable producers to design packaging solutions that satisfy environmental and performance requirements.
Ensuring Stronger and More Reliable PET Preforms
The mechanical strength, thermal stability, and stress resistance of preforms are all significantly impacted by the grades of PET resin. For premium bottles and containers that can survive the rigors of packaging applications, choosing the right resin grade is essential.
Manufacturers are discovering new methods to improve PET performance while advancing sustainability as a result of ongoing improvements in resin technology. PET preforms can be made to satisfy the highest durability standards by a plastic manufacturing company that places a high priority on innovation and quality control. This will enable the company to provide dependable and long-lasting packaging solutions for a variety of sectors.
What's Your Reaction?
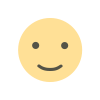





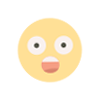