Plastic Injection Molding Costs: Factors, Breakdown, and Cost-Reduction Strategies
Plastic Injection Molding Costs: Factors, Breakdown, and Cost-Reduction Strategies
Plastic injection molding is a widely used manufacturing process for producing high-quality plastic parts in large volumes. However, the cost associated with plastic injection molding can vary significantly based on multiple factors. Understanding these costs and finding ways to optimize them can help businesses save money while maintaining production efficiency. In this article, we will explore the key factors affecting plastic injection molding costs, a breakdown of cost components, and strategies to lower expenses without compromising quality.
Factors Affecting Plastic Injection Molding Costs
Several factors contribute to the overall cost of plastic injection molding. These include:
1. Mold Design and Complexity
The design and complexity of the mold play a crucial role in determining costs. More intricate designs with fine details, undercuts, and multiple cavities require advanced mold-making techniques, increasing the overall expense.
2. Material Selection
The type of plastic material used in injection molding affects the cost. High-performance plastics, such as PEEK or Nylon, are more expensive than standard thermoplastics like ABS or PP. Additionally, material additives like UV stabilizers or flame retardants can increase costs.
3. Mold Fabrication Costs
Creating an injection mold is one of the most significant expenses in the process. Steel molds are durable but costly, while aluminum molds are more affordable but have a shorter lifespan. The choice between single-cavity and multi-cavity molds also influences the cost.
4. Production Volume
The number of parts produced in a single run impacts the cost per unit. High-volume production typically reduces the cost per piece due to economies of scale, while low-volume runs may lead to higher per-unit costs.
5. Cycle Time and Machine Costs
Injection molding machines vary in size and efficiency. Machines with faster cycle times and higher precision tend to be more expensive. The hourly rate of an injection molding machine depends on its tonnage, capabilities, and energy consumption.
6. Labor and Overhead Costs
Labor costs associated with mold setup, maintenance, and production supervision contribute to overall expenses. Overhead costs such as facility maintenance, energy consumption, and quality control also play a role.
7. Secondary Operations
Post-molding operations like trimming, painting, assembly, and packaging add to the total cost. These additional processes should be considered when budgeting for injection molding projects.
Breakdown of Plastic Injection Molding Costs
To better understand how plastic injection molding costs are structured, here is a breakdown of common cost components:
-
Mold Cost: 40-60% of total upfront cost
-
Material Cost: 30-50% of per-part cost
-
Machine and Labor Cost: 20-40% of production cost
-
Secondary Operations: 10-20% of overall cost
-
Overhead Expenses: 10-20% of total manufacturing cost
Strategies to Reduce Plastic Injection Molding Costs
Reducing plastic injection molding costs requires a strategic approach without sacrificing quality. Here are some effective ways to lower expenses:
1. Optimize Mold Design
Simplifying mold design can significantly reduce costs. Minimizing undercuts, reducing part complexity, and using a single-cavity mold for low production runs can help cut expenses.
2. Choose Cost-Effective Materials
Selecting affordable yet durable plastic materials can help balance cost and performance. Discussing material options with a supplier can help find alternatives that meet specifications at a lower price.
3. Increase Production Volumes
Bulk production reduces the cost per unit due to lower setup costs per part. Consolidating multiple orders into a single production run can maximize efficiency.
4. Use Multi-Cavity Molds
While multi-cavity molds require higher upfront investment, they can reduce the per-unit production cost by producing multiple parts simultaneously.
5. Reduce Cycle Time
Optimizing machine settings, using efficient cooling techniques, and selecting faster-curing materials can reduce cycle time, leading to lower operational costs.
6. Minimize Secondary Operations
Designing parts that require minimal trimming, painting, or assembly reduces post-processing costs. Using automation for finishing processes can also enhance efficiency.
7. Select the Right Manufacturer
Choosing an experienced manufacturer with efficient production processes can help minimize costs. Some manufacturers offer bulk discounts, optimized mold designs, and cost-effective material sourcing.
8. Implement Lean Manufacturing Practices
Reducing waste, improving workflow efficiency, and optimizing machine utilization are essential in cutting down unnecessary costs in injection molding.
Conclusion
Plastic injection molding costs depend on multiple factors, including mold complexity, material selection, production volume, and machine efficiency. By understanding the key cost components and implementing cost-reduction strategies, businesses can optimize expenses while maintaining product quality. Whether you are a small business or a large-scale manufacturer, effective cost management in plastic injection molding can significantly impact profitability and long-term success.
What's Your Reaction?
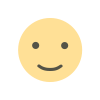





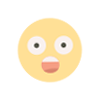