CNC Machining: The Revolution in Manufacturing

In the world of modern manufacturing, precision and efficiency are paramount. The demand for products that are both high-quality and cost-effective has led to the widespread adoption of CNC (Computer Numerical Control) machining. CNC machining is a process that has revolutionized industries across the globe, from aerospace to automotive, medical devices to electronics, by enabling the creation of intricate parts and components with unmatched precision and consistency.
What is CNC Machining?
CNC machining refers to the use of computers to control machine tools that create precise parts and components from a variety of materials, including metals, plastics, and composites. Unlike traditional machining, where operators manually control the machinery, CNC machining relies on pre-programmed computer software to automate the entire process. This allows for complex shapes and designs to be executed with high levels of accuracy and speed.
The CNC machining process involves several key steps:
- Design Creation: The process begins with the design of the part using CAD (Computer-Aided Design) software. This design is translated into a digital file, typically in a format like DXF or STL, which can be read by CNC machines.
- Tool Selection: Based on the material and desired outcome, the operator selects the appropriate cutting tools and fixtures for the CNC machine.
- Programming: The CAD design is then converted into G-code, which provides the CNC machine with specific instructions on how to cut, drill, mill, or turn the material to create the desired shape.
- Machining: The CNC machine executes the instructions by moving the cutting tools along the designated axes with extreme precision. Multiple passes may be required to achieve the desired finish.
- Inspection and Quality Control: After machining, the finished product is carefully inspected using tools such as coordinate measuring machines (CMM) to ensure it meets the required tolerances.
Types of CNC Machines
There are several different types of CNC machines, each designed for specific applications and types of material. Here are the most common types:
-
CNC Milling Machines: CNC milling machines are equipped with rotary cutters that remove material from a workpiece. These machines can create a wide range of parts, including gears, brackets, and housings. Milling machines are especially useful for creating complex geometries with multiple features.
-
CNC Lathes: CNC lathes are used to rotate a workpiece while a cutting tool is applied to shape it. Lathes are ideal for creating cylindrical parts such as shafts, bolts, and bushings. CNC lathes are highly effective for producing parts with symmetrical shapes and fine surface finishes.
-
CNC Drilling Machines: As the name suggests, CNC drilling machines are designed for drilling holes into materials. These machines are highly accurate, making them essential for tasks that require precise hole placement, such as in the aerospace or automotive industries.
-
CNC EDM (Electrical Discharge Machining): CNC EDM machines are used to machine very hard materials or create extremely intricate features. This process uses electrical discharges to erode material, allowing for the creation of detailed and precise shapes that are difficult to achieve with traditional cutting methods.
-
CNC 3D Printers: While technically not a "machining" process in the traditional sense, CNC 3D printing is a rapidly growing area of manufacturing. These machines use additive manufacturing techniques to build parts layer by layer, making them ideal for prototyping and creating custom or low-volume parts.
Benefits of CNC Machining
The advantages of CNC machining are vast and contribute to its popularity across multiple industries. Some of the most notable benefits include:
-
High Precision and Accuracy: CNC machines can achieve tolerances down to the micrometer, ensuring that parts are produced with a high degree of accuracy. This is essential for industries such as aerospace, where even the smallest deviation can have catastrophic consequences.
-
Consistency and Reproducibility: One of the most significant advantages of CNC machining is its ability to replicate the same part over and over with identical specifications. Once a program has been set, the CNC machine can produce thousands of identical parts without any variation, ensuring consistency and reducing the need for manual intervention.
-
Complex Geometries: CNC machining can produce parts with intricate geometries that would be difficult or impossible to achieve with manual machining. This includes parts with sharp angles, complex curves, and detailed features, such as undercuts or holes in hard-to-reach areas.
-
Speed and Efficiency: CNC machines operate much faster than manual machines, and they can run 24/7 with minimal downtime. This leads to faster production times and lower labor costs, ultimately making it a more efficient process for high-volume manufacturing.
-
Cost-Effectiveness: While the initial investment in CNC equipment can be significant, the ability to automate and produce high-quality parts quickly and efficiently often results in significant cost savings. Additionally, the reduction in errors and waste leads to further savings over time.
-
Material Flexibility: CNC machines can work with a wide variety of materials, including metals, plastics, ceramics, and composites. This versatility makes them suitable for a broad range of industries and applications.
Industries That Benefit from CNC Machining
CNC machining has found applications in virtually every industry that involves the creation of complex, high-precision parts. Some of the major industries that benefit from CNC machining include:
-
Aerospace: The aerospace industry demands parts with extremely tight tolerances and high-performance materials. CNC machining allows manufacturers to produce components such as turbine blades, landing gear parts, and fuselage components with exceptional precision.
-
Automotive: CNC machining is essential in the automotive industry for producing components like engine blocks, transmission parts, and brake systems. The ability to create high-performance, durable parts is critical in ensuring the safety and reliability of vehicles.
-
Medical Devices: The medical industry relies on CNC machining for the production of implants, surgical instruments, and diagnostic equipment. CNC machines allow for the creation of complex and biocompatible parts, meeting the stringent requirements of the medical field.
-
Electronics: Many electronic devices, such as smartphones, computers, and consumer electronics, rely on CNC-machined components. These parts often require tight tolerances and precise features, which CNC machining is perfectly suited for.
-
Defense and Military: CNC machining is critical in the defense sector for producing high-precision components for weapons systems, military vehicles, and aerospace equipment. These parts must meet rigorous specifications to ensure functionality and safety.
-
Consumer Goods: From kitchen appliances to furniture, many consumer goods are manufactured using CNC machining. It allows for mass production of high-quality, aesthetically appealing products with consistent quality.
The Future of CNC Machining
As technology continues to evolve, so too does CNC machining. One of the most exciting developments is the integration of AI and machine learning into CNC systems. These advancements will lead to even more automation, faster machining speeds, and enhanced decision-making capabilities. Additionally, additive manufacturing technologies, such as 3D printing, will continue to converge with traditional CNC machining, enabling hybrid manufacturing solutions that combine the best of both worlds.
The demand for CNC-machined parts is only expected to grow as industries continue to prioritize precision, efficiency, and customization. With advances in materials, software, and machinery, the possibilities for CNC machining are limitless, making it one of the most important technologies in modern manufacturing.
Conclusion
CNC machining has transformed the way industries produce parts and components, offering unmatched precision, efficiency, and versatility. Whether in aerospace, automotive, medical devices, or any other sector, CNC machining continues to push the boundaries of what is possible in manufacturing. As technology advances, CNC machining will only become more essential in meeting the growing demands of the global market. The future of manufacturing is CNC, and it’s a future that promises innovation and excellence at every turn.
What's Your Reaction?
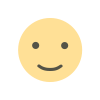





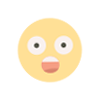